-
Aluminum Alloy Casting
-
Pressure Die Casting Mould
-
Metal Casting Molds
-
Aluminium Die Casting Mould
-
EPS Foam Mould
-
Lost Foam Mould
-
Sand Casting Mould
-
Permanent Mold Casting Aluminum
-
Aluminium Gravity Die Casting
-
Die Cast Aluminum Tooling
-
Auto Parts Mould
-
Multi Cavity Mold
-
Cylinder Head Mold
-
High Precision Mold
-
Rapid 3d Printing Service
-
Greg HenkThanks for your kindly hospitality. Your company is very professional , we will have nice cooperation in the near future.
-
Lionel LoboGood company with nice service and high quality and high reputation. One of our reliable supplier , goods are delivered in time and nice package.
Reducer Shell Pressure Die Casting Mould Heat Treatment
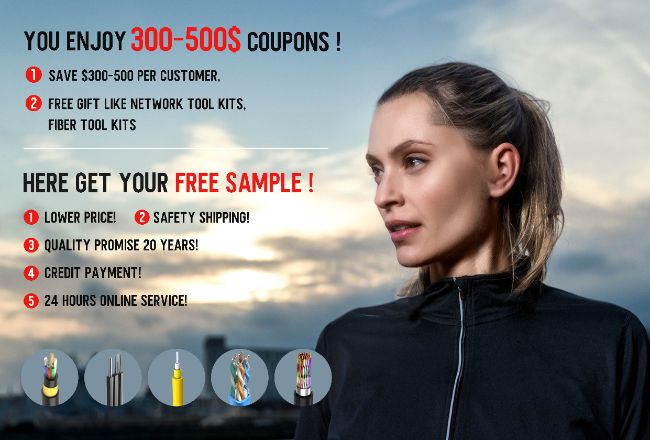
Contact me for free samples and coupons.
WhatsApp:0086 18588475571
Wechat: 0086 18588475571
Skype: sales10@aixton.com
If you have any concern, we provide 24-hour online help.
xName | Pressure Die Casting Mould | Product Material | Aluminium A380 |
---|---|---|---|
Product | Reducer Shell | Surface Treatment | Heat Treatment >HRC45 |
Average Wall Thickness | >3mm | Customized | Customized Size |
Mould Life | 500,000-1,000,000 Shots | Using Hardness | >HRC45 |
Highlight | Shell Pressure Die Casting Mould,Reducer Shell Pressure Die Casting Mould,Heat Treatment Pressure Die Casting Mould |
Reducer Shell Pressure Die Casting Mould Heat Treatment
Die Casting Mould is typically made from high-quality steel alloys that offer good hardness, toughness, and wear resistance. The most commonly used materials for die casting molds include:
- H13 Tool Steel: This is the most commonly used material for die casting molds due to its excellent combination of hardness, toughness, and thermal fatigue resistance.
- NAK80 Tool Steel: NAK80 is a pre-hardened steel that offers excellent dimensional stability and wear resistance, making it ideal for producing high-precision parts.
- 8407 Tool Steel: This material is highly resistant to heat, wear, and corrosion, and is often used in high-pressure die casting applications.
- Aluminum: Some low-volume or prototype die casting molds may be made from aluminum to reduce costs and lead times. However, aluminum molds have a shorter lifespan than steel molds.
Pressure Die Casting Mould Parameters
Mold Base | LKM C50 + P20 for AB, Cast iron etc. |
Inserts(cavity and core) | Dievar, H13, 8407, 1.2344 or the material you required |
Standard | HASCO, DME, MISUMI, PUNCH and so on |
Product Material | ADC12, ADC14, A360, A380, AlSi9Cu3 and so on |
Mold Treatment | Heat Treatment >HRC45 |
Product Surface | Sand blasting, Powder coated, Painting, Anodizing, etc |
Shape & Color | Can be design according to your needs |
Process | High Pressure Die Casting |
Certificated | ISO 9001:2015 Certificated |
Our Advantages
1. We are the biggest lost foam mould manufacturer in China, we focus on high challenge lost foam mould and we have large gantry machining centers,30 sets imported high speed machining center,more than 40 sets general machine tool equipment;
2. We have 36 senior mould designers, to ensure reasonable / safety / high efficiency mould design and ensure the fast mould delivery and rational mould structure, make the process more safer and the production efficiency more higher;
3. We using numerical control machine tool to manufacture the mould cavities, to ensure a even thickness ;
4. We using ZL104 Aluminium to casting the mould, to manufacture a high strength mould;
5. For the big mould, we using Ø22*1 copper tube as cooling pipe, with water spray system, to get a nice cooling effect;
6. We Have (TEF10N) coating on the mould surface, it can reduce the friction, anti water/static electricity/acid-base/high-temperature, with this we can ensure the pattern has smooth surface without distrotion, and easy to demould;
7. All the screws we using stainless steel screw, easy to disassemble during maintenance;
8. For the big mould chest, we using 18-20mm thick wrought aluminium plate, to offer high strenght cavity ;
9. For the complex mould which is difficult to demould, we can manufacture the automaitc mould with take out device ;
10. We produce the pattern sample to customer after finish the mould, when the pattern was qualified, then we do exceptance job for the mould ;
11. We have the Hexagon coordinate measuring instrument imported from the Switzerland to have a test make sure our mould qualified.
About Us
While leading the Chinese brand, Luoyang Liushi mould develop the international market positively, we export a large number of molds to the United States, India, Taiwan and other countries. We have become an international first-class lost foam mould supplier and we have manufactured mould for Germany's machine Teubert and American molding machine Vulcan.
The research and development center is consist of 36 designers who are expert in 3D design, mold design, NC programming craftsmen, lost foam casting craftsmen and so on. We provide a full range of design and services for you. We discuss the mould process and confirm the scheme with your engineer together, this can guarantee the mould structure more reasonable more safety and more efficiency. We finish the product model and detection through reserve scan and 3D Coordinate Measuring technology to make sure each customer satisfy their mould.
We have lost foam casting process and gravity casting process. There are 2 automatic casting production lines of lost foam process, 1 production line of T6 heat treatment, 1 set EPS foaming machine, 2 sets 1000kg centralized melting furnaces, 6 sets 600kg graphite crucible furnaces, 1 set automatic HS - CXJ - 3200 high efficiency and energy-saving molding machine, 16 sets of other model white pattern molding machine, 1 set plain bumper with the same advanced performance as American Fukang brand, 1 set density equivalent meter, 1 set Fosco dusting machine; 2 sets Aluminum alloy gravity pouring and turning machine, 3 sets Coated sand core-making machine , 1 set X-ray flaw detection spectrometer, 1 set Metallographic analyzer, and more than 20 sets of other corollary equipment. Not only we can supply with Aluminum Alloy Castings , but also we can supply with machined finished parts. The capacity of Aluminum Alloy Gearbox Casing Castings can reach up to above 10000 tons every year. The reliable products passing rate of 95%.