-
Aluminum Alloy Casting
-
Pressure Die Casting Mould
-
Metal Casting Molds
-
Aluminium Die Casting Mould
-
EPS Foam Mould
-
Lost Foam Mould
-
Sand Casting Mould
-
Permanent Mold Casting Aluminum
-
Aluminium Gravity Die Casting
-
Die Cast Aluminum Tooling
-
Auto Parts Mould
-
Multi Cavity Mold
-
Cylinder Head Mold
-
High Precision Mold
-
Rapid 3d Printing Service
-
Greg HenkThanks for your kindly hospitality. Your company is very professional , we will have nice cooperation in the near future.
-
Lionel LoboGood company with nice service and high quality and high reputation. One of our reliable supplier , goods are delivered in time and nice package.
High Hardness Aluminium Die Casting Mould Chroming Anodizing
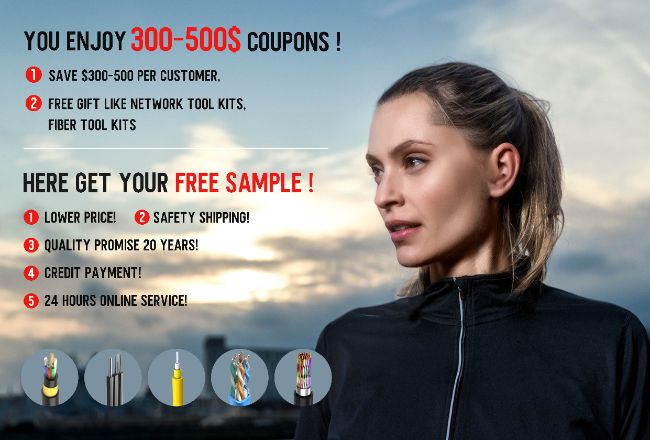
Contact me for free samples and coupons.
WhatsApp:0086 18588475571
Wechat: 0086 18588475571
Skype: sales10@aixton.com
If you have any concern, we provide 24-hour online help.
xProduct Name | High Hardness Aluminium Die Casting Mould | Customized | Yes |
---|---|---|---|
Demoulding | Automatic | Using Hardness | >HRC45 |
Mould Life | 500,000-1,000,000 Shots | Average Wall Thickness | >3mm |
Highlight | high hardness aluminium die casting mould,chroming anodizing aluminium die casting mould,high hardness aluminum die casting mold |
High Hardness Aluminium Die Casting Mould Chroming Anodizing
Aluminium Die Casting Foundry Features
-
Material: Die casting molds are typically made of high-quality steel, such as H13 steel, due to its excellent thermal conductivity, hardness, and durability.
-
Mold Design: The mold design is crucial for successful die casting. It includes factors such as the part shape, draft angles, gating system, cooling channels, and ejection mechanism. A well-designed mold ensures the production of high-quality parts with minimal defects.
-
Mold Cavities: The mold cavities determine the number of parts that can be cast simultaneously. The size and complexity of the part influence the number of cavities in a mold. Multi-cavity molds can produce multiple parts in each casting cycle, increasing productivity.
-
Cooling System: Efficient cooling is essential to achieve shorter cycle times and maintain dimensional accuracy. Cooling channels are integrated into the mold to rapidly extract heat from the molten metal. Proper cooling ensures consistent part quality and reduces the risk of defects.
-
Mold Maintenance: Regular maintenance of the mold is necessary to ensure its longevity and optimal performance. This includes cleaning, lubrication, and inspection for any signs of wear or damage. Timely repairs or replacements are necessary to avoid production delays.
-
Mold Cost: The cost of an aluminum die casting mold can vary depending on its complexity, size, and number of cavities. Molds are typically more expensive to manufacture compared to other casting processes due to the precision required and the materials used.
-
Mold Life: The lifespan of an aluminium die casting mold depends on various factors, including the number of cycles, the quality of maintenance, and the type of alloy being cast. High-quality molds can last for thousands or even tens of thousands of cycles before requiring refurbishment or replacement.
Aluminium Die Casting Foundry Parameters
Material Capability | Aluminum,Zinc,Brass,Iron,Carbon steel, Stainless steel, etc. |
Surface Treatment | Shot blast, beat blast, powder coating, painting, zinc plating, hot dip galvanized, electrophoreses..etc |
Product Weight | 0.01KG-50000KG |
Casting Tolerance | CT3-CT9 |
Trade Terms | FOB |
Packing | single polybag, bubble bags,wooden case,carton box..etc |
Delivery terms | 15-45days for bulk |
Manufacture Process
1. Review the part design,drawings and quality standard from clients.
2. Mould and Tooling design & manufacturing
3. Mould and Tooling testing & confirm the sample
4. Die casting raw castings
5. Surface treatment: Trimming,Deburring, polishing, cleaning, passivation & power coating and other requirement from Customer
6. Precision machining: CNC lathes, milling, drilling, grinding etc
7. Full Inspection
8. Packing
9. Delivery
Our Advantages
1. We are the biggest lost foam mould manufacturer in China, we focus on high challenge lost foam mould and we have large gantry machining centers,30 sets imported high speed machining center,more than 40 sets general machine tool equipment;
2. We have 36 senior mould designers, to ensure reasonable / safety / high efficiency mould design and ensure the fast mould delivery and rational mould structure, make the process more safer and the production efficiency more higher;
3. We using numerical control machine tool to manufacture the mould cavities, to ensure a even thickness ;
4. We using ZL104 Aluminium to casting the mould, to manufacture a high strength mould;
5. For the big mould, we using Ø22*1 copper tube as cooling pipe, with water spray system, to get a nice cooling effect;